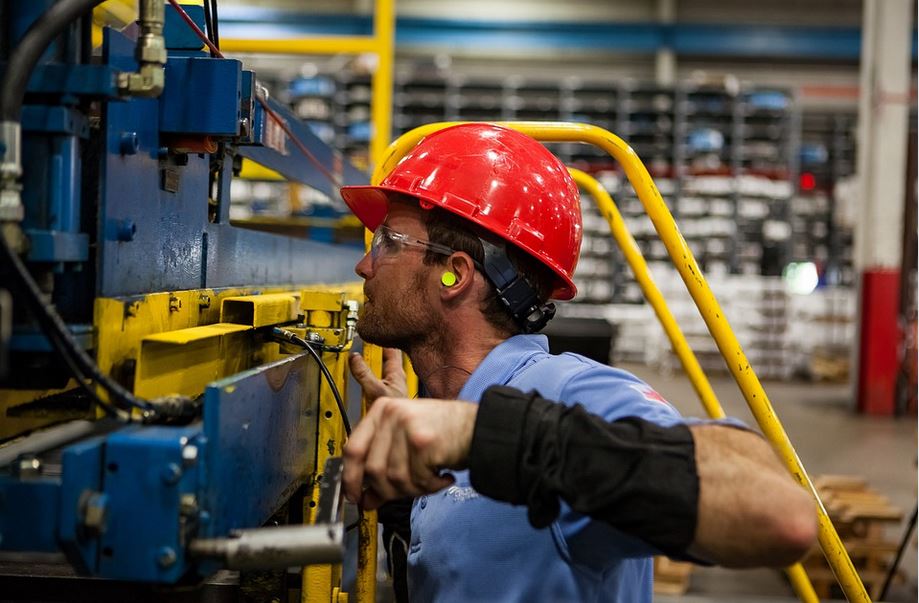
It seems like an easy thing to understand right? Of course skills and equipment need to constantly be evolving in manufacturing if you are to succeed. However, look at the biggest manufacturers of cars in the world. Look at Mercedes, BMW, Ford and Honda. All of them were caught with their pants down, when Tesla started to rise. They didn’t invest in machine learning robots, AI in their manufacturing process, they didn’t invest in battery technology as much as Tesla and now look. Governments are demanding cars be fully electric by 2030 and Tesla is at least 5-10 years ahead in the tech race. This is why your equipment and skills need to evolve constantly. But how do you do this?
Annual review and managers
Managers get paid to make sure they are constantly watching over the equipment their teams are using. It’s normal for a manufacturing manager to inspect equipment before, during and after use in an 8-hour shift. However, they aren’t always allowed to be part of the annual review of how equipment is performing and could be improved and or replaced. This is not something you should be doing. You need to have a consultation with all of your managers when it comes to the annual review of where the equipment is failing and ask them if they have any ideas of how it could be improved.
Go to expos
Going to business events for manufacturing equipment is simply crucial to your success. Here you find out what kinds of improvements the very brands you buy from, are making and or have made. For example AKRS Equipment provides landscaping, farming and gardening equipment to clients of all kinds. They are constantly evolving their fleet, improving their relationships with manufacturers, giving feedback and listening to the concerns of their own clients. This type of method of operating is exactly what your business should be doing if you work in manufacturing. Having very close relationships with brands who make your equipment is critical for your manufacturing to keep evolving, getting better in every way.
Invest in skills
There is nothing more important than the investment in your employees. Even if you have sub-par equipment, the skills of your employees will bring out the best in them. This is because skills gaps are always going to be worse than equipment gaps. A team of employees that is up to date with modern manufacturing techniques, materials, tests and uses of equipment, is always going to find a way to meet deadlines and objectives. So give your employees training every two years or so, and your managers should be receiving updates to their knowledge annually. This keeps workers and leaders always in lockstep.
Evolving your equipment has to be done with the evolution of employee skills. It’s vital you do both at the same time. Go to expos and meet your suppliers and brands face to face and make sure your annual review of equipment is comprehensive and includes managers, not just the C-suite!
No comments yet.